
Firstly: PPL means: „Preferred parts list“, or all the company part numbers (=CPN), which you – as buyer, as electrical engineer, or as you working on the pick & place machine – like to see again in new designs. Or vice versa: Which CPN’s do you like to get rid of for various reasons?
You might ask yourself: ”Is it worth reading this article to the bottom?” Spoiler: Yes, it is, and: A thoroughly managed PPL saves you time and money. In times of material shortages, this can add up into the percent-range of your annual direct material spend.
In case your company has only one single production plant, with only one single CPN per part(function): Well you are the few lucky guys out there and it might not affect you that much.
However, if you are overseeing several locations, multiple design centers and some company acquisitions over the years: PPL might be a sharp tool for you.
Why don’t you count the number of CPN’s for some real simple components: The 1Kilo Ohm 0402 1% resistor, or the 32KHz clock crystal. If you are ending up in a number greater than 2: Please continue reading!
Assuming you ended up counting with 50 different CPN’s for clock crystals: That can’t be by purpose, or? They might have been accumulated over the years.
The exciting question is: „How to get rid of 48 of them?”
The initiative: “One should do a board re-spin. For all PCB’s” remains wishful thinking.
However, at least for NPI designs: From all those 50, only 1 – 2 should be seen in NPI design, means: always the same 1 – 2. So, we need a selection list. And we are at the PPL already.
Without a PPL: Designers will randomly pick one out of the 50 parts. There is no chance to see this number decreasing
With a consistently applied PPL: The number will slowly decrease.
Benefits:
– Bigger purchasing volumes with fewer CPN’s. Better prices.
– Easier exchange of stock between factories, especially in case of production shutdowns, production relocations or passing on of IOS (=Inactive, Overstock, Surplus).
– Easier setup of placement machines. (I have seen setups where one placement machine was set up with 4 feeders, same manufacturer part, just 4 different CPN’s).
– It is the least costly, possibly even the only viable way to get rid of redundant CPN’s. Do you have an estimate of how much it costs to maintain a CPN? Like 1000 … 2000USD? This makes savings from a PPL calculable, decisions can be made objectively.
– Negotiations with manufacturers of a component group become much easier.
Criteria to make it as CPN into the Olympus of the PPL
Each R&D site will say: Standard? Gladly! As long as standard means: “Our CPN’s”. An agreement on a common standard will be much easier in terms of argumentation and company policy if the criteria are defined objectively and comprehensibly for all.
- Surface mount, never through hole.
- At least 2, better more approved manufacturer parts per CPN, see an earlier article on the AMPL.
- Yes, exceptions apply.
- No, the 2nd reel size on the same manufacturer part is NOT a second source.
- RoHS III compliant plus whatever is relevant for your products.
- The life cycle of the components should still be longer than n years. You determine “n” yourself based on the typical life of your products. SiliconExpert has the information.
- Purchasing must have a fair chance to buy the manufacturer parts, i.e. there is a stable supply chain.
- Production must be able to assemble the parts process-safe.
- The part size for the passives (= the chicken food) should be 0402 or smaller. Think back to the MLCC capacitor crisis.
- If all this applies to several CPN’s, choose the part with the best price or the highest quantity.
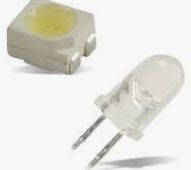
And how is this enforced?
1) One person in the company owns the PPL. Usually in component engineering.
2) NPI BOMs are checked for PPL. The more components in the BOM are found in the PPL, the better. Define a minimum percentage: 80% is a good start. Don’t threaten trouble, just offer a reward for the highest density of PPL parts in a design.
3) Any existing CPN must be clearly categorized: In the PPL or not, or at least „PARDO“ = Preferred, Acceptable, Restricted, DoNotUse, Obsolete.
4) The determination for a CPN = „PPL part or not“ must be made as early as possible, ideally before the part is placed into the schematic by the layout people. After that, the resistance of the NPI people to change it later will go to infinity.
By the way:
If you take the maintenance costs of a CPN of about 1000USD seriously, do the math if:
– Having 10 different CPN’s for 1 microcontroller / 10 HEX files programmed by the distributor is worthwhile – or better having 1 unprogrammed CPN, and program as a part of the in-circuit test?
– The differently labeled screw terminals can possibly be printed internally.
– You have 2 different part numbers for a commercial-grade and an industrial-grade. It may or may not be worth it. With the maintenance costs, you can determine that cleanly.
Now:
Get to grips and start a PPL.
As always: Ask me, I’m happy to help.